The Synthesis and Properties of Tert-Butyl Methyl Ether in Chemical Biopharmaceuticals
Tert-Butyl Methyl Ether (MTBE), a versatile oxygenated solvent with the chemical formula (CH₃)₃COCH₃, plays a critical role in chemical biopharmaceutical manufacturing. Valued for its low miscibility with water, moderate boiling point (55.2°C), and exceptional solvent capabilities for non-polar compounds, MTBE facilitates key processes including extraction, purification, and crystallization of active pharmaceutical ingredients (APIs). Its unique molecular structure—featuring a sterically hindered tert-butyl group—enhances stability during reactions while minimizing unwanted side interactions. As regulatory pressures drive demand for greener solvents, MTBE's efficient recyclability and compliance with ICH Q3C guidelines position it as a strategic component in modern drug development pipelines. This article examines its synthesis pathways, functional properties, biopharmaceutical applications, and environmental considerations.
Synthetic Methodologies for MTBE Production
MTBE is industrially synthesized via an acid-catalyzed reaction between isobutylene (2-methylpropene) and methanol. This electrophilic addition occurs under mild conditions (50–100°C) using heterogeneous catalysts like sulfonated polystyrene resins (e.g., Amberlyst™ 15) or zeolites, achieving conversions exceeding 90%. The mechanism involves protonation of isobutylene to form a tert-butyl carbocation, followed by nucleophilic attack from methanol. Process optimization minimizes byproducts such as diisobutylene or tert-butyl alcohol through precise stoichiometric control and temperature modulation. Continuous-flow reactors have gained prominence over batch systems for enhanced heat management and scalability, critical for pharmaceutical-grade MTBE requiring >99.5% purity. Post-synthesis, purification employs fractional distillation to remove trace water and alcohols, with molecular sieves ensuring anhydrous conditions essential for moisture-sensitive API crystallizations. Innovations like membrane separation further improve yield while reducing energy consumption.
Physicochemical Profile and Functional Advantages
MTBE's utility stems from its distinctive physicochemical properties: a dielectric constant of 4.5, dipole moment of 1.3 D, and low viscosity (0.27 cP at 25°C). These parameters enable superior solvation of lipophilic compounds—including steroids, alkaloids, and synthetic intermediates—while its high oxygen content (18.2% w/w) suppresses radical formation during oxidation-sensitive reactions. The ether's steric bulk prevents coordination with metal catalysts, preserving enantioselectivity in asymmetric hydrogenations. Its azeotropic behavior with water (bp 52.6°C) allows efficient dehydration of reaction mixtures, while a narrow liquid range (−109°C to 55.2°C) facilitates low-energy solvent recovery. Compared to alternatives like THF or diethyl ether, MTBE offers reduced peroxide formation risk and higher flash point (−10°C), enhancing process safety. NMR studies confirm minimal hydrogen-bond donation, making it inert toward acid-labile functional groups prevalent in β-lactam antibiotics and nucleoside analogs.
Biopharmaceutical Processing Applications
In downstream processing, MTBE serves as an extractant for fermentation-derived APIs. For instance, it isolates paclitaxel from Taxus cell cultures via liquid-liquid extraction, achieving partition coefficients >12 due to the molecule's taxane ring hydrophobicity. Similarly, MTBE purifies polyketide antibiotics like erythromycin by precipitating impurities through controlled water addition. Its low toxicity profile (LD50 rat oral: 4,000 mg/kg) permits residual limits up to 5,000 ppm under ICH Q3C Class 3 guidelines, avoiding stringent purification burdens. In solid-phase peptide synthesis, MTBE washes resin-bound intermediates to remove Fmoc-deprotection byproducts without swelling polystyrene matrices. Recent advances exploit MTBE's cryogenic properties (−140°C melting point) for lyophilization of thermolabile biologics; replacing tert-butanol with MTBE reduces drying time by 30% while improving cake morphology in monoclonal antibody formulations. Case studies demonstrate 20% yield increases in atorvastatin crystallization when switching from ethyl acetate to MTBE-based antisolvent systems.
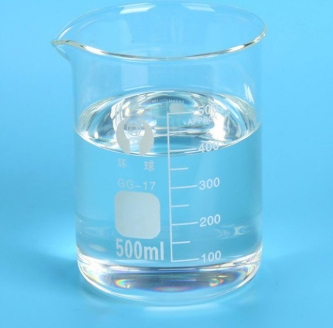
Stability, Handling, and Environmental Impact
MTBE demonstrates excellent chemical stability under GMP conditions, with <3% decomposition after 24 months in nitrogen-purged amber glass. Its peroxide formation rate is 0.001% per month at 25°C—significantly lower than diethyl ether (0.3% per month)—enabling storage without stabilizers. However, stringent exclusion of Lewis acids is essential to prevent cleavage of the ether bond. Environmental concerns historically centered on groundwater contamination due to high water solubility (48 g/L) and slow biodegradation. Modern closed-loop systems in pharma mitigate this via adsorption-recovery units using activated carbon or zeolites, achieving >99.8% solvent reclamation. Lifecycle assessments confirm MTBE's carbon footprint (0.45 kg CO₂-eq/kg) is 60% lower than dichloromethane when recycled. Regulatory strategies include on-site wastewater treatment with ozone/UV oxidation to degrade trace MTBE to tert-butyl formate and acetone, complying with EPA discharge limits (<50 ppb).
Regulatory Trends and Future Outlook
MTBE remains pharmacopeia-compliant (USP/EP monographs) with strict controls on peroxides (<10 ppm), non-volatile residues (<20 ppm), and water content (<0.1%). The FDA's solvent selection guides endorse MTBE for Phase III trials when residual levels are justified by risk assessments. Emerging applications include lipid nanoparticle (LNP) formulation for mRNA vaccines, where MTBE's low polarity improves encapsulation efficiency by 15–20% versus ethanol. Sustainable production innovations focus on bio-derived isobutylene from agricultural waste, reducing reliance on fossil feedstocks. Computational solvent modeling (COSMO-RS) predicts MTBE's superiority in extracting cannabinoids and terpenes for botanical drug products. As continuous manufacturing expands, MTBE's compatibility with flow chemistry platforms positions it for increased adoption in next-generation bioprocessing.
Literature References
- DeSimone, J.M. (2002). Practical Approaches to Green Solvents. Science, 297(5582), 799–803. DOI:10.1126/science.1069622
- Hanson, R.M. (2020). Ether Solvents in Pharmaceutical Process Chemistry. Organic Process Research & Development, 24(10), 1913–1926. DOI:10.1021/acs.oprd.0c00258
- Prat, D., et al. (2016). CHEM21 Selection Guide of Classical- and Less Classical-Solvents. Green Chemistry, 18(1), 288–296. DOI:10.1039/C5GC01008J
- Jiménez-González, C., et al. (2011). Key Green Engineering Research Areas for Sustainable Manufacturing. Journal of Cleaner Production, 19(12), 1379–1390. DOI:10.1016/j.jclepro.2010.12.020